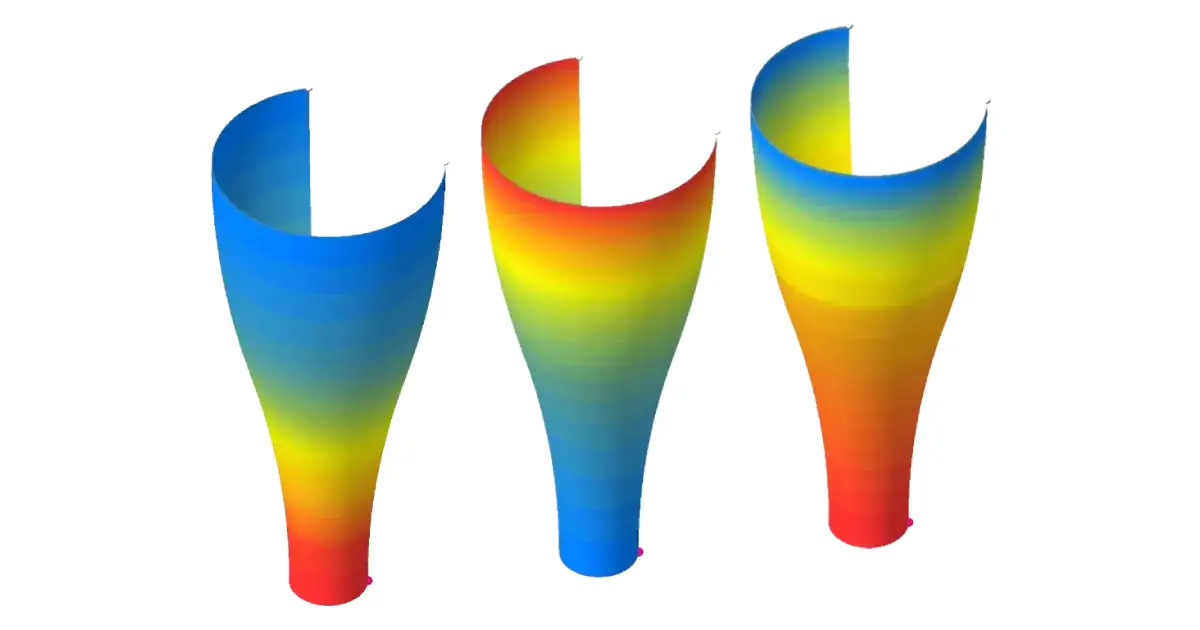
Optimize your Bubble Cooling
Are you involved in film blowing or stretch tube production? Are you facing challenges with bubble stability? Would you like precise data on temperatures, velocities, thicknesses, and other physical properties throughout the entire bubble length?
The VEL™ system includes a specialized module for simulating bubble behavior during the film blowing (or tube stretching) process. This module enables you to:
- Design the bubble’s shape
- Optimize temperature development both along and across the bubble
- Estimate thickness, velocity, deformation, stress, and curvature
- Identify stability problems
We are excited to announce the release of the new VEL™ 7.0 Bubble Cooling Module.
What can the module do?
Simply define the bubble shape, select your materials, and set your cooling conditions. At every point along the bubble, the module provides data on:
- Temperature
- Material velocity
- Film thickness
- Tension in all directions
- Deformation in all directions
- Bubble curvature
- Phase state: where the material is molten, solidifying, or fully frozen
Example 1: Single-layer Bubble (Material: LDPE)
Temperature distribution along the bubble for different pulling speeds.
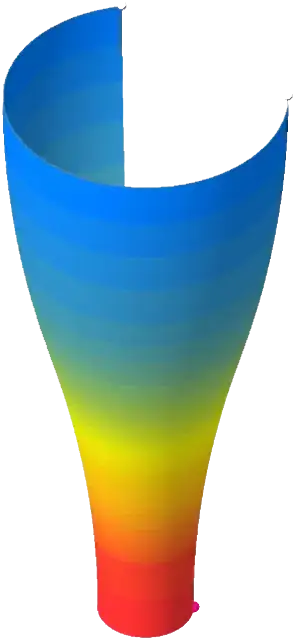
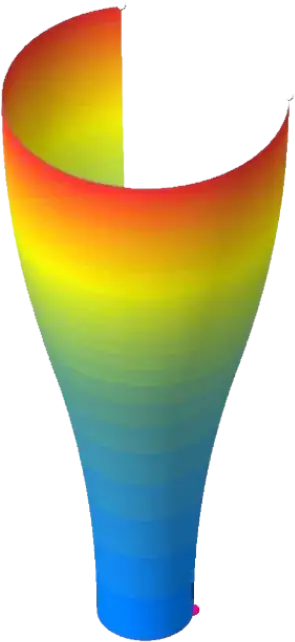
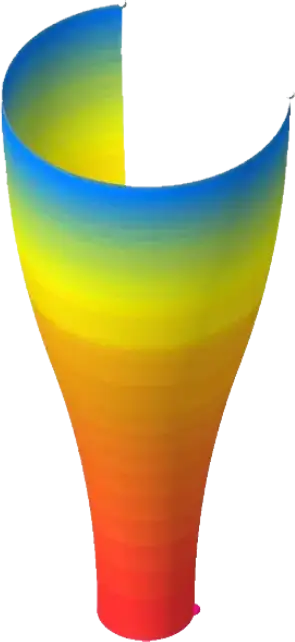
The figure shows temperature distribution along the bubble, including the cooling sleeve (left). The module clearly identifies which sections of the bubble remain molten, are in the process of solidifying, or have already solidified (right).
This simulation capability applies to both single and multi-layer film structures.
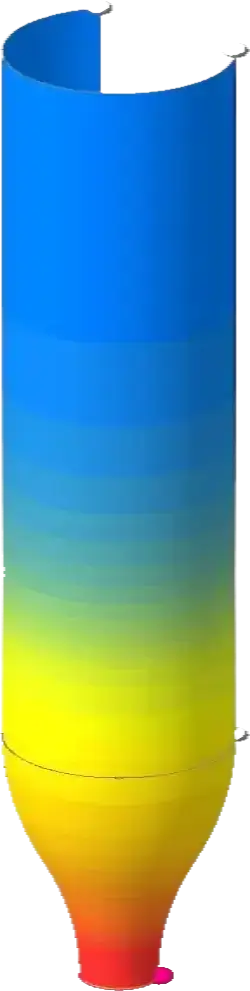
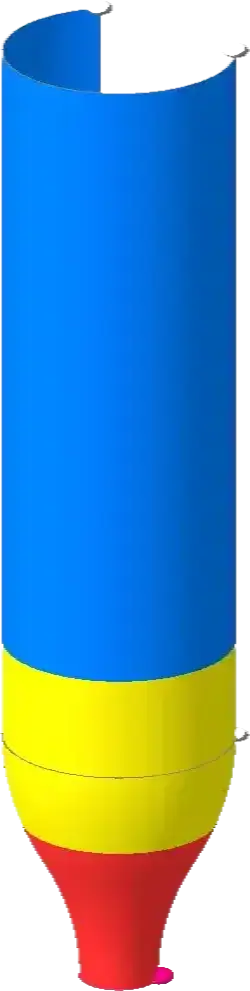
Example 2: Multi-layer Bubble
In coextrusion processes, the module helps to compensate for the varying solidification behavior of different materials (with different melting/freezing temperatures).
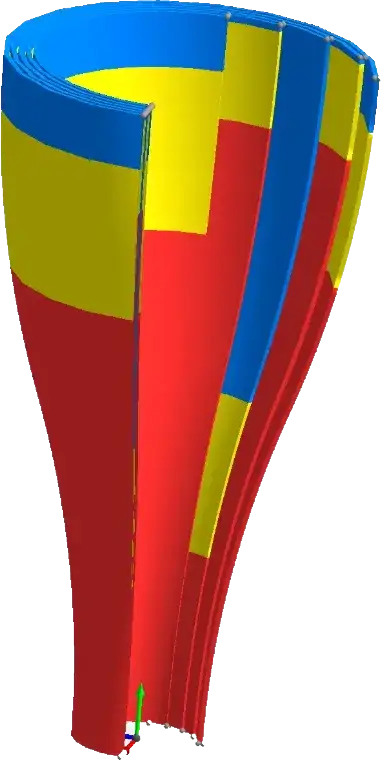
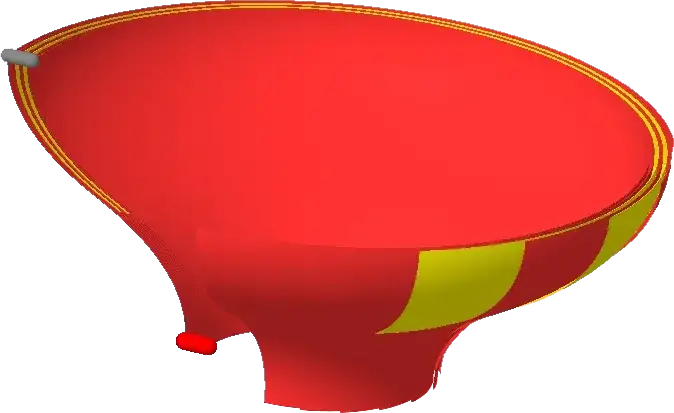
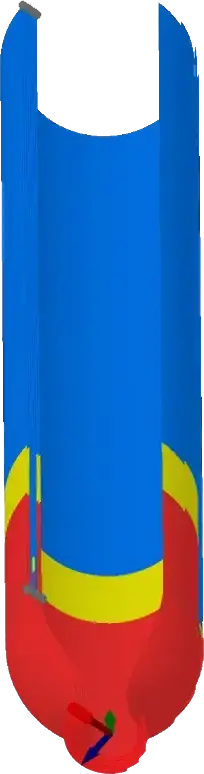
Materials used: LDPE 25% / Adhesivum 7% / Polyamide 12% / EVOH 12% / Polyamide 12% / Adhesivum 7% / LDPE 25%.